Global Market Size, Forecast, and Trend Highlights Over 2025-2037
Solar PV Market size was valued at USD 397.65 billion in 2024 and is poised to cross USD 7.08 trillion by the end of 2037, expanding at more than 25% CAGR during the forecast period i.e., between 2025-2037. In 2025, the industry size of solar PV is assessed at USD 476.54 billion.
Photovoltaic manufacturing capacity moved from the U.S., Europe, and Japan to China in the past few decades. China has invested more than USD 50 billion in its domestic PV production and supply capacity - ten times more than Europe. Presently, China’s production share of all PV components exceeds 80% and is expected to reach 95% during the forecast period.
Solar power has transitioned from an emerging and niche technology to a mature and mainstream industry over the past decade. By the end of 2035, solar power is projected to supply 40% of U.S. electricity demand, thereby, accelerating the decarbonization of transportation, construction, and manufacturing industries. Solar energy adoption has the potential to yield workforce development and economic growth. The industry currently employs over 230,000 people in the U.S., at an average wage equivalent to the national average for comparable positions and the U.S. solar industry is likely to employ 500,000-1500,000 individuals by 2030.
Various factors shape the impact of resilience measures on PV projects. Module capital expenditure and capacity factors significantly impact project development costs. China produces PV modules at lower costs than other economies. This results from a local material sourcing, highly integrated, and largely consolidated domestic supply chain. Moreover, the manufacturers in the country operate on low electricity rates and subsidized land and factory infrastructure. The primary threat to the cost competitiveness of U.S. and European PV producers is energy prices that weigh heavily as compared to China's PV production market. To address this challenge, investments in R&I are set to accelerate the adoption of manufacturing technologies with better throughput and higher energy efficiency.
IEA reported that in 2023, around 446 GWdc of PV was deployed worldwide, bringing cumulative PV capacity addition so far to 1.6 TWdc. With China’s dominance in the global market, a whopping 60% of installations came from the country in 2023, while Italy and Germany showcased a 2x growth in installations. The rest of the world experienced a 30% y-o-y growth and the U.S. held the second-largest market share in terms of annual deployment and installations. Research Nester analysts project that cumulative global photovoltaic installations will reach up to 5 TWdc by 2030 and 15 TWdc by 2050. Mono c-Si technology-based PV shipments were 35% in 2015 and reached 98% in 2023, while n-type mono c-Si was 63% of total PV shipments, increasing from 5% in 2019 to 51% in 2022.
PV System and Component Pricing:
The median system costs of large-scale utility-owned photovoltaic systems in 2023 was USD 1.27/Wac (relatively flat since 2018) and the residential PV systems by median price as reported by EnergySage reached USD 2.8/Wdc, a 6.3% y-o-y surge. Global polysilicon spot prices in 2023 as of late April were USD 6.76/kg, which was a 22% drop from mid-January (USD 8.70/kg), thus, registering the lowest price observed over the last decade. The recent slump in module prices worldwide leveled off at USD 0.11/Wdc in Q1 2024. The U.S. average module price in Q4 2023 was USD 0.31/Wdc, representing a 5% q-o-q and 22% y-o-y decrease in the country module pricing.
Solar PV Market: Key Insights
Report Attribute | Details |
---|---|
Base Year |
2024 |
Forecast Year |
2025-2037 |
CAGR |
25% |
Base Year Market Size (2024) |
USD 397.65 billion |
Forecast Year Market Size (2037) |
USD 7.08 trillion |
Regional Scope |
|
Supply chain mapping
Component manufacturing and trade dynamics in key countries
Solar PV is a cornerstone of clean electricity generation and overarches the goal of achieving sustainable energy transition and net-zero emission by 2050. The PV supply chain starts with the refinement of polycrystalline silicon or polysilicon, derived from metallurgical-grade silicon (MGS) and crystalline silicon (c-Si). Approximately, 96% of global PV module shipments in 2020 used c-Si technology, made from melting polysilicon chunks into ingots, slicing them into thin wafers, and converting the wafers into PV cells and PV modules. Other PV modules use cadmium telluride (CdTe) technology, with higher adoption in the U.S. (16% compared to 4% worldwide) and c-Si representing the other 84%.
The U.S. PV Supply Chain Dynamics:
Solar photovoltaics play a pivotal role in the U.S. efforts to reduce GHG emissions and minimize the impact of climate change. Decades of innovation and significant cost reductions so far have made PV one of the most affordable forms of electricity generation. In regards to, decoupling from China’s raw material supply and its influence in the U.S. manufacturing sector, the country is striving to bring PV supply chain in-house. The U.S. has a certain thin-film CdTe module production capacity that does not rely on obtaining raw materials from China. Over 16% of CdTe module installations are all supplied by a single U.S. company that also produced one-third of those CdTe modules in the U.S. Given the rate at which the economy is inching toward decarbonization, it is unlikely that any alternate technology, including CdTe, could fully displace conventional electricity generation before 2050.
Solar power represented 5% of the energy generation capacity addition in 2010 and as of 2024, its share rose to 58%, accounting for a whopping 36.4 Gw of 62.8 Gw total electricity generated in the U.S. (almost double of 18.4 Gw in 2023). As described in the follwing graph, it is estimated that in a business-as-usual case, the global shipments will reach 200 GWdc by 2030, and in global decarbonization scenario, it could grow to over 500 GWdc by 2030.
Domestic Production of Feedstocks, Ingots, and Wafers in 2022
Key Players/ Manufacturers |
Process & technology |
Total Production (Tones) |
DC Alabama |
Silicon feedstock |
42,000 |
Globe Metallurgical |
Silicon feedstock |
16,000 |
Mississippi Silicon |
Silicon feedstock |
36,000 |
WVA Manufacturing |
Silicon feedstock |
73,000 |
Globe Metallurgical |
Silicon feedstock |
24,000 |
Hemlock Semiconductor Corporation |
Polysilicon (Siemens) |
32,000 |
Wacker Polysilicon |
Polysilicon (Siemens) |
19,000 |
REC Silicon |
Silanes |
2,000 |
CubicPV |
c-Si Wafers |
Not Available (20 MWdc/yr capacity) |
Despite this growth, electricity decarbonization in the U.S. would require a significant acceleration of annual PV deployment. In an aggressive grid decarbonization scenario, the country’s deployment growth is likely to quadruple by the end of 2030 from 19GWdc in 2020. SEIA reported 40.3 GWdc of PV was installed in 2023 and a cumulative of 186.5 GWdc. 22 states registered a 5% electricity generation from solar, with California accounting for the highest of 28.2%. However, solar still represented a mere 5.6% of annual generation and 11.2% of net summer capacity in 2023In 2023, 26.0 GWh / 8.8 GWac of energy was stored onto the electric grid, which was a 34% y-o-y surge. That being said, in business-as-usual scenario, global shipments are estimated to reach 200 GWdc and in total decarbonization case, it could grow beyond 500 GWdc by 2030.
Strategies, Actions, and Recommendations:
Production Tax Credit (PTC) and Investment Tax Credit (ITC) are the primary framework policies in the U.S. However, the most prominent change in direct support policies was implemented in 2022 with the introduction of the Inflation Reduction Act (IRA), a federal law for loans, grants, and tax credit expansions. This has been pivotal for small- and large-scale PV manufacturing and installations in a socially equitable manner. The law has sanctioned USD 370 billion in investments and U.S. EPA’s GHG Reduction Fund has allocated USD 7 billion in grants.
The IRA offers the following solar production incentives:
Component |
Tax Credits |
Solar cells |
$0,04/watt |
Wafers |
$12/m3 |
Polysilicon |
$3/kg (must be 99.9% pure) |
Backsheets |
$0,40/m2 |
Modules |
$0,07/watt |
Inverters |
Varies |
Torque tubes (trackers) |
$0,87/kg |
Structural fasteners |
$2,28/kg |
Source: The European Technology and Innovation Platform for Photovoltaics
Summary of the tax credits applicable to PV within the scope of IRA. MPTC = Manufacturing Production Tax Credit, PTC = Production Tax Credit, ITC = Investment Tax Credit, GHG = greenhouse gas
Source: The European Technology and Innovation Platform for Photovoltaics
The c-Si module assembly began in the U.S. in 2018 using imported cells and by 2020, a 4.3 GWdc of PV modules was assembled with 24% over 2019. This growth was primarily led by First Solar’s strategic doubling of production capacity. As the PV demand continues to grow, more opportunities to further domestic manufacturing are set to surface. In the wake of import restrictions implemented in 2021, potentially traceable to China-based companies will inevitably strengthen the U.S. PV supply chain. Some of the prominent polysilicon companies in the country include Michigan-based Hemlock (with 35,000 MT of annual production capacity); Wacker (with 20,000 MT) operating in Tennessee; REC Silicon (with a 16,000 MT plant in Washington and 4,000 MT capacity plant in Montana) and Alabama-based Mitsubishi, (with 1,500 MT). Hemlock, REC, and Wacker have been awarded tax credits under Section 48C, which subsequently helped in the expansion of polysilicon production capacity.
According to the EIA, the U.S. retail electricity sales were USD 3,861 billion, a notable rise from USD 66 billion in 2022. Retail sales comprise net imports or imports minus exports of electricity from Mexico and Canada.
Electricity sales to U.S. retail-electricity customers and percentage shares of total sales (2023)
End user |
Sales in volume (USD billion kWh) |
Shares |
Residential |
1,455 billion kWh |
38% |
Commercial |
1,375 billion kWh |
36% |
Industrial |
1,025 billion kWh |
27% |
Transportation |
7 billion kWh |
<1% |
U.S. electricity share percentages, by provider type (2022)
Electricity providers have been bifurcated into two groups including full-service providers, which supply bundled electricity services, and other providers. Full-service providers typically provide autonomously generated electricity or outsourced from other independent power producers. These include investor-owned utilities such as publicly traded stock electric utilities, public entities such as state power agencies, municipalities, and municipal marketing authorities, federal entities comprising power marketers and producers either financed or owned by the federal government, and cooperatives that are owned by and operated by cooperative members.
The percentage shares of electricity sales, by provider type (2022)
Provider type |
Electricity sales share |
Investor-owned utilities |
75% |
Public and federal entities |
16% |
Cooperatives |
13% |
Others |
15% |
In addition to end-use customers' sales, electricity is often traded on wholesale markets or via bilateral contracts.
U.S. solar investments through 2023:
U.S. solar manufacturing and storage investments reached a record high in 2023, owing to both public and private funding. A comparative analysis of 2023 and 2022 has been provided in the following table.
Investment area |
2023 |
Solar manufacturing |
$5.1 billion (+470% from 2022) |
Battery manufacturing (vehicle and stationary) |
$33.9 billion (+240%) |
Large-scale solar deployment |
$35.4 billion (+45%) |
Large-scale storage deployment |
$17.0 billion (+71%) |
Distributed electricity and storage deployment |
$21.6 billion (+18%) |
Source: U.S. Energy Information Administration, Preliminary Monthly Electric Generator Inventory
In 2024, the total energy produced added up to approximately 62.8 GW of new utility-scale electric-generating capacity which registered a steep surge from 18.4 GW in 2023. Solar held the largest share of new capacity, followed by battery storage. 50% of the overall solar capacity is accounted for by Texas (35%), California (10%), and Florida (6%). Besides the three states, Nevada’s Gemini solar facility which is expected to be commissioned in 2025, will allow a value addition of 690 MW of photovoltaic capacity and 380 MW of battery storage. Furthermore, the U.S. battery storage capacity reached approximately 89% in 2024, with an extended capacity of 30 GW. This is a 705 rise from the 6.4 GW new battery storage capacity in 2023. The Inflation Reduction Act has also accelerated the energy storage development with investment tax credits (ITCs) for stand-alone storage. Prior to the IRA, batteries qualified for federal tax credits only if they were co-located with solar.
China’s influence on global solar photovoltaics:
97% of silicon wafer production is done in China and a major volume is then shipped to other countries as raw material for solar cells. Approximately 75% of the silicon solar cells integrated into modules and deployed in the U.S. are manufactured by Chinese subsidiaries in Southeast Asian countries, including Malaysia, Vietnam, and Thailand. Furthermore, a large volume of PV-component supply comes from China. While a minority but a considerable portion of polysilicon, cells, and modules are sourced outside of China, the global photovoltaic supply chain is significantly dependent on wafers and ingots from China. In addition, other pieces of the module supply chain, comprising manufacturing equipment and balance-of-module components (for example, aluminum frames and glass) are predominantly supplied from China. The local manufacturers account for a key balance-of-PV-system component share, including inverters used in electrical grids) as well as steel and aluminum used for mounting PV modules.
Our in-depth analysis of the solar PV market includes the following segments:
Product |
|
End use |
|
Deployment |
|
Grid |
|
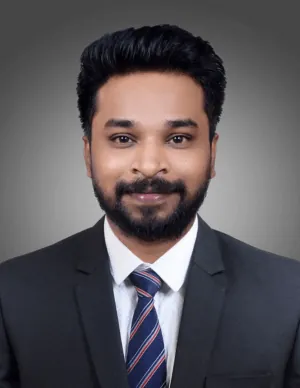
Vishnu Nair
Head - Global Business DevelopmentCustomize this report to your requirements — connect with our consultant for personalized insights and options.
Comparative Analysis of Manufacturing Capacity of PV Components:
A top-down analysis of Polysilicon production
High-purity polysilicon is typically obtained by refining metallurgical-grade silicon, which is used to make solar wafers, silicones, semiconductors, and aluminum alloys. To ensure supply and purity levels MGS suppliers often backward integrate and own a significant portion of the quartz mines. Furthermore, MSG processing is typically energy-intensive, making it imperative to be produced in locations with abundant and affordable electricity sources such as Malaysia, Norway, the U.S., and the Xinjiang region of China. Presently, China dominates that market with over 70% of the worldwide MGS production capacity, and ten Chinese companies account for 35% of domestic capacity, whereas the top five hold approximately 25%.
Principal MGS manufacturing locations & production capacity (Thousand Metric Tonnes)
Source: the U.S. DOE
North America MGS production by top contenders (2022)
MGS Plant |
Manufacturing Capacity (Tonnes) |
Quebec Silicon Becancour, QC |
50,000 |
Ferroglobe Niagara Falls |
30,000 |
Ferroglobe Beverly, OH |
16,000 |
Ferroglobe Alloy, WV |
75,000 |
Dow Corning Mt. Meigs, AL |
42,000 |
Ferroglobe Selma, AL |
31,000 |
Mississippi Silicon Burnsville, MS |
36,000 |
The primary use case of polysilicon is photovoltaic (comprising 80% of the demand) and the other is semiconductors and consumer electronics. Despite there being several polysilicon production techniques, two general approaches are ascribed to the largest market shares. The fluidized bed reactor (FBR) method accounts for 3%-5% of the market share and the Siemens chemical vapor deposition method holds a 90% share. The Siemens process entails the passage of silane precursor or gaseous trichlorosilane (TCS) over the heated silicon filaments. Recovered compounds are further processed to synthesize polysilicon. Virtually all polysilicon manufacturing capacity lies within 10 countries, with China capturing 72% of the global capacity.
The presence of key supplies in China is instrumental in determining component costs, including polysilicon. As per EIA, polysilicon prices increased threefold from USD 6.27/kg in June 2020 to USD 28.46/kg in June 2021. This is ascribed to a supply/demand imbalance owing to wafer and cell manufacturing capacity expansion. With polysilicon emerging as a critical bottleneck, downstream entities such as cells and wafer producers have been strategically stockpiling polysilicon supplies to meet the anticipated demand, largely driven by the proliferation of utility-scale deployment in China. Based on announced projects, polysilicon manufacturing is expected to double down in capacity over the next few years. Some of the new plants built have manufacturing capacities of 30,000-70,000 MT per year, and there are anticipated plans to build facilities with more than 100,000 MT capacities.
Chinese companies have been keen on lowering polysilicon prices by establishing manufacturing facilities and manufacturing in areas with affordable land, electricity, and laborcosts. Western provinces have a considerable build-out including Inner Mongolia, Quinghai, Sichuan, and especially, Xinjiang. It currently hosts China’s 54% and 39% of global production. Based on active projects till 2022 an estimate of China’s overall solar PV component yield is mentioned below.
China’s low labor costs and concentrated c-Si PV supply chain, have posed an entry barrier for other players. In the U.S. labor expenditure represents 22% of the manufacturing costs versus 8% in China, 36% of wafer manufacturing costs in the U.S. versus 23% in China, and 33% of cell manufacturing costs in the U.S. versus 8% in China.
c-Si and CdTe production and global trade:
More than 75% of the c-Si and CdTe modules imported by the U.S. in 2020 came from just three Southeast Asian countries- Vietnam, Malaysia, and Thailand, and the remainder from South Korea. These Southeast Asian countries rely heavily on an upstream Chinese supply chain. The U.S. as of 2020 had limited silicon solar cell operating capacity. However, the following upstream manufacturing in the U.S. gained traction and proved pivotal in the country’s surging solar demand. According to the SEIA, 8.6 GW worth of installation was completed in 2019, showcasing a 21% year-over-year growth.
Source: NRELupdate of (Smith et al. 2021)
Owing to gaps in the global PV supply chain such as high capital expenditure and labor costs, virtually all c-Si raw materials and components are imported to western nations from Southeast Asian countries. These import costs add around 11% to the total manufacturing expenses. A build-up in the domestic PV supply chain would significantly reduce these costs. There are pathways to cut down the cost delta with automation in wafer and ingot assembly lines. In February 2024, First Solar announced its plans to invest USD 10 billion in CdTe thin film in the United States. Retrospective figures from 2023 added USD 2.75 billion in value to the module production capacity, USD 900 million in economic value, and USD 2 billion in output.
Ingots and Wafers
Ten Chinese companies manufactured 98% of the overall solar wafers in 2020, of which three companies- LONGi, GCL, and Zhonghuan garnered 71% of the produced capacity. From 2016 to 2020, the abovementioned companies grew their collective capacity to 173 GWdc (58% of global capacity) from 29 GWdc (29% of global capacity). This trend was followed by the rapid growth in monocrystalline PV modules market share.
Furthermore, seven Chinese provinces were ascribed to 10 GWdc of wafer production capacity. Notably, Jiangsu, located in the north of Shanghai, accounted for 28% of China’s total wafer capacity, while outside of China, East Asia contributes 10 GWdc of global wafer capacity. China-based Jinko Solar announced its plans to build a 7 GWdc wafer and ingot facility in Vietnam. This aims at streamlining cell production operations in Malaysia and module assembly in the U.S. The company stated initiation of the project was made in 2020, to bypass U.S. trade restrictions on import materials. This strategic expansion underscores the company’s efforts to build a robust supply chain while navigating the changing trade dynamic.
Module and Cells
Since the implementation of new manufacturing tax credits, there has been a significant influx of investments to build and expand the entire solar module supply chain, including ingots, modules, wafers, and cells. Prior to the enactment of the federal manufacturing incentives, there was roughly 16.6GW or 41,500 MT/year polysilicon capacity and 7 GW/year of module capacity. Cell manufacturing was onshored for the first time since 2019, and it is expected that additional cell capacity will come online by the end of 2025. To date, there has been a steep growth in module production, climbing from 7 GW before the federal manufacturing tax credits to 44.4 GW in December 2024, marking a rise of over 500%.
The total U.S. module supply chain including operational, under-construction, and announced projects reached an estimated value of 81.6 GW. The establishment of PV module supply chain is a sluggish process due to conformance periods, permits, construction, and commissioning. The further up the supply chain ladder, the longer the building time. New factory expansions are anticipated to continue over the next several years.
India in 2022 was the only country to witness a major fall in imports from China, underpinning a fall of 76% or -7.5 GW y-o-y. A total slump of 9.8 GW from 2.3 GW was observed in the first half of 2022. Moreover, stringent government regulations including the imposition of tariffs resulted in a shift away from imports to domestic manufacturing capacity utilization. India’s local solar module production capacity has stepped up since then and India has set a benchmark in global solar module and panel exports Türkiye.
Despite the ongoing efforts to decouple from the reliance on China for component supplies, China’s solar panel export spiked by 34% in the first half of 2023. This is pivotal in meeting the high energy demand in Europe and South Africa. The rising focus in clean energy transition has further increased dependency on China’s solar exports. Out of the 90.4% export volume, Europe emerged as the biggest importer (58%), followed by Brazil receiving 9.5 GW of solar panels made in China in the first half of 2023. Africa is projected to witness the fastest import growth rate of 187% as the government is seeking ways to mitigate the rising energy crisis, while China is heavily capitalizing on the prevailing demand-supply gap.
China’s solar exports in the first half of 2023, share (%) in $ value terms
Export destination |
Export Share |
Europe |
52.5% |
Brazil |
7.6% |
Pakistan |
3% |
Australia |
2.6% |
Japan |
2.7% |
South Africa |
2.7% |
Saudi Arabia |
2.1% |
Rest of World |
11.1% |
Source: Ember Energy
The exponential growth in the solar PV market is positively influencing the global semiconductors market. In 2022, devices were the world's 33rd most traded product, with an overall trade of USD 87.7 billion. Between 2021 and 2022 photovoltaic/photosensitive/LED semiconductor grew by 21.9%, from USD 72B to USD 87.7B, representing 0.37% of total world trade.
Yearly growth of Photovoltaic & LED Semiconductor Devices global trade
Year |
Trade value |
2019 |
$56B |
2020 |
$57.4B |
2021 |
$72B |
2022 |
$87.7B |
Source: OEC
Photovoltaic/LED Semiconductor Devices Global Trade
Country |
Exports |
Imports |
||
|
Total Trade Value |
Market Share |
Total Trade Value |
Market Share |
China |
USD 44.7 Billion |
51% |
USD 6.6 Billion |
3.19% |
Vietnam |
USD 6.83 Billion |
7.79% |
USD 693 Million |
1.55% |
Malaysia |
USD 4.92 Billion |
5.61% |
USD 321 Million |
0.72% |
Japan |
USD 4.01 Billion |
4.57% |
USD 2.05 Billion |
4.58% |
Germany |
USD 3.52 Billion |
4.01% |
USD 5.03 Billion |
5.73% |
The U.S. |
USD 2.08 Billion |
2.37% |
USD 13.2 Billion |
15.1% |
Source: OEC
Photovoltaic End of Life (EOL)
Rising focus on decarbonizing electricity grids has proportionately ramped up solar energy generation and storage capacities across the world. For context, to meet decarbonization goals, the U.S. must install 30 GWac every year from 2025 to 2030. 19 GW of solar capacity was installed in 2021 and the cumulative capacity has reached 100 GW in the U.S. This signifies that installation of new systems is likely to surge at a steep rate in the forthcoming years.
While the lifespan of a PV system is about 25-35 years, some system components including modules are already entering the waste stream. Moreover, modules reach end-of-life owing to weather damage, manufacturing serial defects, or installation errors. Yearly PV module EOL volume reach up to 12% of the annual municipal electronic waste in the United States by the end of 2050. 99% of PV module materials are non-hazardous and 95% are fully recyclable with available technologies. This sets a robust foundation for low-impact and safe EOL material handling methods. Presently, EOL handling processes are unfavorable to recycling. PV modules recycling cost to waste generators is $15-$45 per module, which is significantly higher than the landfill fee of $1-$5 for each module. This in turn is likely to impact federal and state policies on how waste is processed.
Source: IRENA
Action Plan Coverage
In June 2021, the Solar Energy Technologies Office (SETO) issued an RFI to solicit feedback from the PV waste management communities regarding key challenges in EOL processing. The responses, expert interviews, and literature reviews were used to identify potential research areas to streamline and optimize PV EOL practices. Responses emphasized the role of policy in EOL handling and developing separation technologies to enhance materials recovery.
With stakeholder input on prevalent challenges in hardware design, data collection and analysis, and identifying DOE’s role in EOL management, SETO, in 2021 rolled out a five year action plan.
The 2021 multi-year program plan was established based on the 2021 PV EOL workshop and RFI feedback. It focuses on the following enablers of a circular economy:
- Data gathering & analysis: Based on modeled waste volume and handling, the need for realistic collection, sorting, transportation, and materials reclamation is evident. SETO aims to establish a standalone database with 10 MW of PV EOL data collected by the end of 2025 and implement comprehensive data standards. Furthermore, non-confidential data will be made publicly accessible to the waste management, solar, and policy communities.
- Hardware development & process research: SETO emphasizes improving the raw materials and energy usage efficiency to, in turn, minimize the resources required to process EOL materials and extend component lifespan. It recommends steel, Cu, and Al be sold to scrap metal markets at EOL. However, recovering silver from the metallization and separating polymers and composites including back sheets are some of the areas, where materials recovery may be challenging. Research into enhancing the recovery rate, while minimizing the recovery cost burden is expected to help shift the economics of solar PV recycling.
Companies Dominating the Solar Photovoltaic Market
- First Solar
- Company Overview
- Business Strategy
- Key Product Offerings
- Financial Performance
- Key Performance Indicators
- Risk Analysis
- Recent Development
- Regional Presence
- SWOT Analysis
- Tata Power Solar Systems Ltd.
- Canadian Solar Inc.
- Wuxi Suntech Power Co. Ltd
- Nextera Energy Sources LLC
- BrightSource Energy Inc.
- SunPower Corporation
- Vivaan Solar Pvt. Ltd.
- Waaree Group
- Jinko Solar
- OMCO Solar
Recent Developments
- In November 2024, Trinasolar announced that its larger-area 350.4 cm² n-type bifacial TOPCon industrial solar cells achieved an efficiency of 2658% in the n-type TOPCon Cells category. This is the 28th record-breaking mark that Trinasolar has established as a world record in cell/module conversion efficiency, further underscoring the its robust innovation capabilities.
- In September 2024, U.S. DOE in tandem with kWh Analytics introduced a USD 2.4 million initiative to develop solar PV projects. The new initiative will enable the collection of real-world electricity loss data from renewable power grids and aid in presenting new standardization for minimizing power generation loss.
- In September 2024, OMCO Solar and Heleine collaborated to launch bundled PV modules for the U.S. market. The bundled solution supports local solar developers pursuing the lucrative tax credit under the IRA.
- Report ID: 6098
- Published Date: Nov 15, 2024
- Report Format: PDF, PPT
- Get detailed insights on specific segments/region
- Inquire about report customization for your industry
- Learn about our special pricing for startups
- Request a demo of the report’s key findings
- Understand the report’s forecasting methodology
- Inquire about post-purchase support and updates
- Ask About Company-Level Intelligence Additions
Have specific data needs or budget constraints?
Solar PV Market Report Scope
FREE Sample Copy includes market overview, growth trends, statistical charts & tables, forecast estimates, and much more.
Connect with our Expert