Automotive Aluminum Extrusion Market - Historic Data (2019-2024), Global Trends 2025, Growth Forecasts 2037
Automotive Aluminum Extrusion Market in 2025 is assessed at USD 97.19 billion. The global market size exceeded USD 91 billion in 2024 and is set to expand at a CAGR of over 8.5%, surpassing USD 262.8 billion revenue by 2037. Asia Pacific is on track to record USD 113.79 billion by 2037, driven by increasing industry requirements for materials that increase efficiency and reduce CO2 emissions.
The automotive aluminum extrusion industry is experiencing significant growth owing to the increasing adoption of modular vehicle platforms across the automotive industry. Major automakers have been working to extend the range of electric vehicles in the automotive sector. With the increasing need for reduced vehicle weight, there has been the use of aluminum extrusions in EVs. The EVs promote aluminum extrusion usage, attributed to their lightweight design and flexibility, and these properties support consistent design scalability for various vehicle models, extending the vehicle's operating range. Aluminum extrusions serve companies by allowing detailed design modifications that work perfectly for multiple product halves of a manufacturing operation.
Companies have been forming strategic collaborations to create low-carbon aluminum extrusions for commercial vehicles. For instance, in November 2023, Hydro Extrusions entered a business partnership with Watt Electric Vehicle Company (WEVC) to deliver recycled low-carbon aluminum extrusions suitable for the upcoming WEVC commercial electric vehicle known as the eCV1. The partnership is expected to achieve a significant reduction in vehicle production carbon footprint, compared to the popular electric light commercial vehicles.

Automotive Aluminum Extrusion Sector: Growth Drivers and Challenges
Growth Drivers
- Advanced manufacturing techniques: As the automotive industry transitions to modular platforms, manufacturers implement advanced manufacturing methods, especially regarding aluminum extrusion techniques. Hollow aluminum extrusions together with multi-hollow profiles and high-strength alloys enhance material efficiency and component strength. The combination of 3D printing technology with AI-based manufacturing systems improves their accuracy during extrusion procedures. There has been an increase in the research and development for detecting defects in 3D-printed materials. For instance, in March 2023, researchers at Argonne National Laboratory created an AI-driven detection system that is capable of detecting and predicting defects in 3D-printed materials, thus, enabling more reliable additive manufacturing processes.
- Hybrid vehicles and fuel efficiency: Automotive manufacturers are increasingly adopting aluminum extrusions attributed to rising plug-in hybrid electric vehicles and mild hybrid production. To increase fuel efficiency and lower emissions, the vehicles demand materials that weigh less. Lightweight aluminum extrusions maintain superior strength and make them excellent choices for vehicle structures and crash management systems, along with battery compartments. The implementation of aluminum allows for diminished vehicle weight, enhanced performance, and strict environmental regulations for automakers. The automotive industry is extensively using aluminum extrusions in hybrid vehicles to boost efficiency and sustainability methods. Modern aluminum suppliers are producing stronger and lighter alloy substances along with superior extrusion processes, that keep safety standards unaffected. The aluminum industry is making investments in research to optimize its extrusion methods for hybrid vehicle parts.
Challenges
- Complexity in joining and assembly: Aluminum poses difficulties for joint connections as its lower melting temperature along with its oxide layer formation behavior cannot be welded in conventional ways that steel undergoes. Strong durable connections between materials require unique joining approaches including laser welding and friction stir welding, alongside rivet bonding, as aluminum presents challenges to traditional welding procedures. Specialized welding techniques demand sophisticated equipment and expert employees, that consequently drives up production expenses. The difficult nature of aluminum extrusion assembly functions as a barrier to its broad automotive industry usage especially when cost optimization becomes important.
- Limited high-volume production: Mainstream automotive manufacturers face challenges in achieving high-volume production speed of internal combustion engine vehicles, as the aluminum extrusions mainly appear in premium electric vehicles. Present-day extrusion facilities cannot achieve the necessary production scale, as they operate at slow speeds, leading to more manufacturing expenses. Automakers focusing on efficient mass-market production, face limitations, resulting in a reduction of aluminum extrusions in high-volume vehicle production lines.
Automotive Aluminum Extrusion Market: Key Insights
Report Attribute | Details |
---|---|
Base Year |
2024 |
Forecast Year |
2025-2037 |
CAGR |
8.5% |
Base Year Market Size (2024) |
USD 91 billion |
Forecast Year Market Size (2037) |
USD 262.8 billion |
Regional Scope |
|
Automotive Aluminum Extrusion Segmentation
Type (Sub-structures, Door Beam, Bumpers, Pillars, Sub Frames, Seat Back Bar, Front Side Rail, Space Frames, Body Panels)
Sub-structure segment is poised to hold over 36.5% automotive aluminum extrusion market share by the end of 2037, owing to the requirement of manufacturers for lightweight and durable materials in constructing vehicles. The use of aluminum extrusions in chassis and underbody components leads to vehicle weight reduction, as they reduce the sub-structure weight. This weight reduction brings benefits to fuel efficiency and overall performance.
The automotive market chooses aluminum extrusions, as these components can handle high-stress levels while offering vehicle weight reduction benefits. Mass electric vehicle production benefits from the rising use of aluminum extrusions across the industry. EV manufacturers need aluminum extrusions for their structural components, due to the requirement for lightweight high-strength materials. Adopting aluminum extrusions becomes crucial for sub-structure applications, due to the radical transformation of modern vehicle framework development, and for making it lighter and more efficient.
Vehicle (Mini-compact, Supermini, Compact, Mid-size, Executive, Luxury, Utility Vehicles, Light Commercial Vehicles, Heavy Commercial Vehicles, Buses and Coaches)
The utility vehicles segment in automotive aluminum extrusion market is expected to account for a significant revenue during the forecast period, attributed to the increasing demand for off-road and multi-purpose vehicles. Structural components of utility vehicles need light and strong materials that assure durability, operational efficiency and safety characteristics. Utility sector favors aluminum extrusions, as they offer impressive strength-to-weight ratios, permitting designers to build fuel-efficient vehicles with unaltered structural performance. Automakers use aluminum extrusions to fashion parts, boosting vehicle performance alongside handling while extending vehicle lifespan, as consumers prefer versatile vehicles. The anti-corrosive properties of aluminum metal make it the optimal choice for utility vehicles that function in tough environmental conditions. Global demand for utility vehicles has increased due to simultaneous trends of outdoor activities and rising consumer spending power. The market necessitates new aluminum extrusion production approaches from automakers to develop modern applications.
Our in-depth analysis of the global automotive aluminum extrusion market includes the following segments:
Type |
|
Vehicle |
|
Aluminum Grade |
|
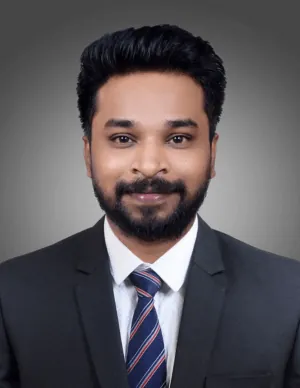
Vishnu Nair
Head - Global Business DevelopmentCustomize this report to your requirements — connect with our consultant for personalized insights and options.
Automotive Aluminum Extrusion Industry - Regional Scope
Asia Pacific Market Analysis
Asia Pacific in automotive aluminum extrusion market is predicted to account for more than 43.3% revenue share by the end of 2037, owing to increasing industry requirements for materials that increase efficiency and reduce CO2 emissions. The automotive industry in the region utilizes aluminum extrusions, as they meet environmental standards through lightweight strength without sacrificing cost-effectiveness. The acceptance of lightweight materials gains momentum as the electric vehicle (EV) and hybrid vehicle production demand weight reduction to enhance battery performance and extend driving distances.
The China automotive aluminum extrusion market is expected to propel, due to the increasing adoption of electric vehicles in the country. The automakers in China are making investments to develop lightweight materials for EVs, as the aluminum extrusions reduce weight while ensuring strength performance. The automotive sector finds aluminum especially beneficial for EV battery enclosures alongside chassis and body components, as it boosts fuel efficiency meeting emission standards. Through continuous financial support from the local government's EV support programs, manufacturers are speeding up their adoption of aluminum materials for the automotive sector.
The automotive aluminum extrusion market in India is expanding, as the manufacturers in the country require lightweight materials to meet environmental regulations while achieving better vehicle fuel efficiency. To manufacture vehicle components including body panels along with structural elements and chassis utilizes extrusions made from aluminum, as these materials possess light weight strength characteristics. Automakers choose to reduce vehicle weight, due to the local government’s emphasis on EV promotion and emissions regulations, enabling higher demand for aluminum extrusions. The domestic growth of electric and hybrid vehicles drives this trend, as aluminum extrusions serve as essential components to build EV battery enclosures as well as frame structures. In addition, the Indian automotive manufacturers are also using advanced manufacturing solutions to make their aluminum extrusion techniques more effective.
North America Market
The North America automotive aluminum extrusion market is expected to witness a rapid expansion between 2025 and 2037. The growth is attributed to the rising electric vehicle (EV) production volume and manufacturers' goal of implementing lightweight materials for superior energy efficiency. The rising electric vehicle production requires additional aluminum extrusions to achieve better weight reduction and enhance battery performance and operating range. The EV transition enables aluminum suppliers to develop specialized EV automotive components through enhanced production of customized extrusions for this sector. Companies are investing to accelerate technological developments in aluminum extrusion manufacturing in the regional automotive sector. Vehicle manufacturers dedicate funds to innovative production processes that include multi-material joining technology and precise extrusion methods to build better and improved solutions. Modern vehicle designs require high-performance aluminum components and technology advances enable the industry to produce these complex parts needed in the market. The automotive industry in the region maintains its strong commitment to aluminum extrusions, as they deliver improved safety and design versatility along with sustainability goals.
The U.S. automotive aluminum extrusion market is increasing, owing to the requirement for sustainable components from automotive industries to boost energy efficiency. The global effort to lower carbon emissions has sparked higher adoption of aluminum materials for vehicle production, as these metals allow manufacturers to fulfill regulatory standards. Vehicle production depends more on aluminum extrusions for structural and safety components, to create lighter but stronger automotive designs. The growing automotive market demand for sustainability and improved fuel efficiency directly increases the need for aluminum extrusions among automotive producers in the country. The automotive manufacturers are forming strategic partnerships, to enhance their aluminum extrusion capabilities. In May 2022, Novelis announced to invest USD 2.5 billion, to build a new low-carbon recycling and rolling plant in Alabama. The facility is expected to have an initial 600 kilotonnes of finished aluminum goods capacity per year.
The automotive aluminum extrusion market in Canada is growing, owing to the local government policies that support green transportation solutions through electric vehicles, to motivate automakers to use aluminum together with other lightweight materials for vehicle construction. Incentives from the local government for electric vehicle consumers and manufacturers creates conditions that accelerate the automotive manufacturers toward aluminum extrusion adoption. Several factors are enabling local suppliers to expand their operations while manufacturers invest more in production facilities for automotive components, supporting the growing demand. Canadian companies involved in automotive aluminum product manufacturing have increased their production of customized lightweight solutions for vehicle structures through their manufacturing facilities. The growth of aluminum extrusion requirements in efficient production systems is expected to strengthen the market.

Companies Dominating the Automotive Aluminum Extrusion Landscape
- Hindalco Industries Ltd.
- Company Overview
- Business Strategy
- Key Product Offerings
- Financial Performance
- Key Performance Indicators
- Risk Analysis
- Recent Development
- Regional Presence
- SWOT Analysis
- QALEX
- Arconic Corporation
- Constellium N.V.
- Norsk Hydro ASA
- Bonnell Aluminum
- China Zhongwang Holdings Ltd.
- ETEM Group
- EMERUS
- ST Extruded Products Germany GmbH
The competitive landscape of the automotive aluminum extrusion market is rapidly evolving, attributed to the integration of advanced technologies in energy management systems by key players. They are focused on developing new technologies and products catering to the stringent regulatory norms and consumer demand. These key players are adopting several strategies such as mergers and acquisitions, joint ventures, partnerships, and novel product launches to enhance their product base and strengthen their market position. Here are some key players operating in the global market:
Recent Developments
- In September 2023, Hindalco partnered with Italian company Metra SpA to develop structured aluminum extrusions. The collaboration is aimed at enabling the production of large-size aluminum extrusion and fabrication technology for building high-speed aluminum rail coaches in India.
- In December 2022, Hydro completed the acquisition of Hueck building systems and extrusion business in Germany. The acquisition is expected to strengthen Hydro’s presence in Germany and other European markets.
- Report ID: 7202
- Published Date: Apr 23, 2025
- Report Format: PDF, PPT
Frequently Asked Questions (FAQ)
- Get detailed insights on specific segments/region
- Inquire about report customization for your industry
- Learn about our special pricing for startups
- Request a demo of the report’s key findings
- Understand the report’s forecasting methodology
- Inquire about post-purchase support and updates
- Ask About Company-Level Intelligence Additions
Have specific data needs or budget constraints?
FREE Sample Copy includes market overview, growth trends, statistical charts & tables, forecast estimates, and much more.
Connect with our Expert